Stringinstruments consist of many individual parts and different types of wood.
We'll be making a poster available for download here soon!
If a violin is made entirely by hand, as we do in celler violin making workshop UEBEL - since 1725 , about 500 individual work steps are necessary to complete a violin.
In terms of pure working time, about 180 working hours are required for this. The drying times of the glues are not included in this number of hours.
The painting is added to this number of hours.
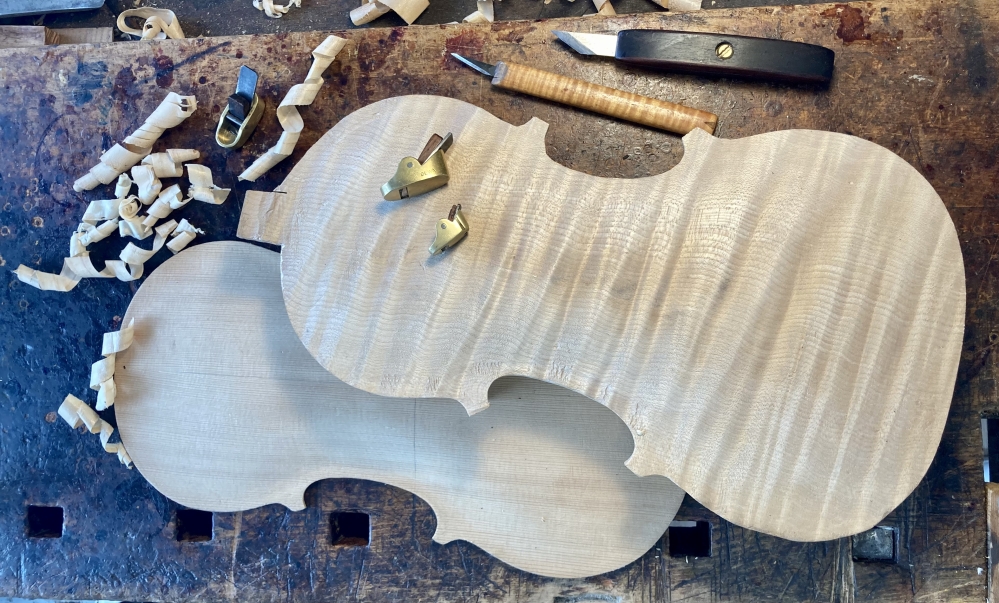
Rosin, also known as bow resin, is made from purified tree resin. The resin is separated into two components by steam distillation. The non-volatile residue is then the rosin. This is then mixed with various substances. Among other things, there are manufacturers who add gold, silver or copper particles to their rosin.
Since rosin produces a lot of dust, some companies are already making "dust-free" rosin for allergy sufferers.
Without the rosin, the bow hairs do not have enough resilience and do not stick to the string, without rosin there is no sound.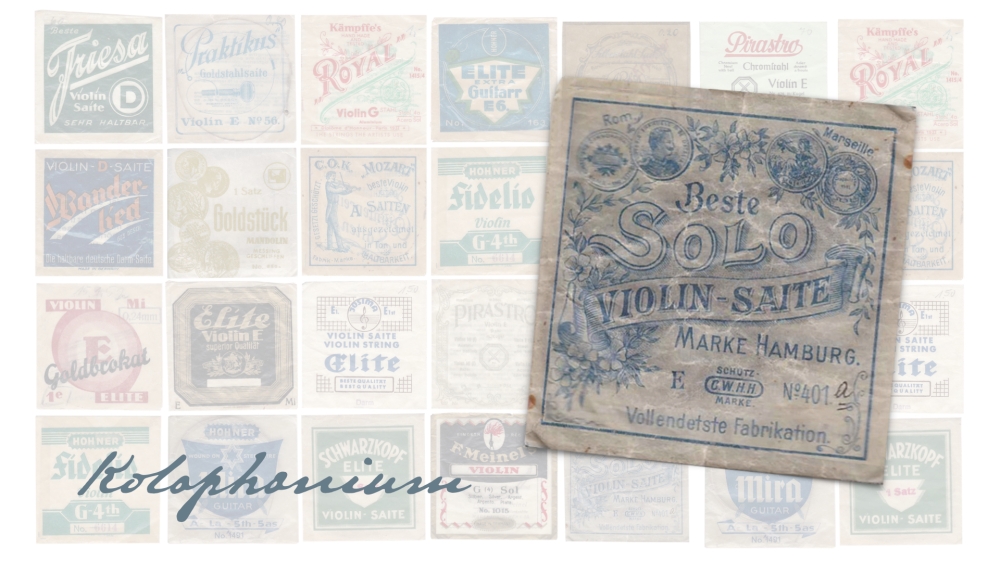
Cremona-born violin maker Andrea Amati is sometimes referred to as the inventor of the violin.
But the ancestors of the violin can be dated back to the 8th century. These precursors include, for example, the Rebec and the Fidel.
Over the centuries, these precursors developed into the violin we know today.
While today's violin has four strings, in the beginning the instrument only had three strings.
From the 16th century, the violin gradually evolved into the instrument we know today, and Andrea Amati definitely contributed to that. Andrea Amati refined the construction of the violin in terms of its shape, curvature and scroll, as well as the choice of wood.
The Italian violin makers in particular had a great influence on the construction of the violin. But it is only since the great success of Antonio Stradivari that increasingly standardized violin models have been built.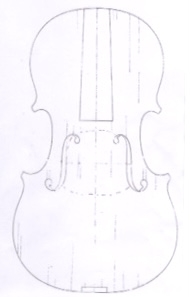
A particularly large number of violin- and musicalinstrument- makers have settled in some German cities.
Bubenreuth
Ever since the Germans were expelled from Czechoslovakia, Bubenreuth has been the center of Franconian stringed and plucked instrument making. Many instrument makers were previously based in Bohemian, Schönbach.
Klingenthal
The town of Klingenthal is known as the cradle of German violin making. From 1659 exiles from Bohemia moved to the Vogtland town. The well-known violin making dynasty Hopf was based in Klingenthal.
Markneukirchen
Bohemian exiles from the border town of Graslitz also settled in Markneukirchen. They brought the art of violin making to Markneukirchen. Around the year 1800, the violin makers in Markneukirchen made about 18,000 violins a year.
Today one of the two German violin making schools is located in Paulus Schlösschen in Markneukirchen.
Mittenwald:
The Bavarian town of Mittenwald was an important center of violin making in the 18th century. But there are still violin makers here today who practice their craft here. There is also a technical school in Mittenwald
violin making.